Anti-Friction CoatingsLubricant for dry lubrication
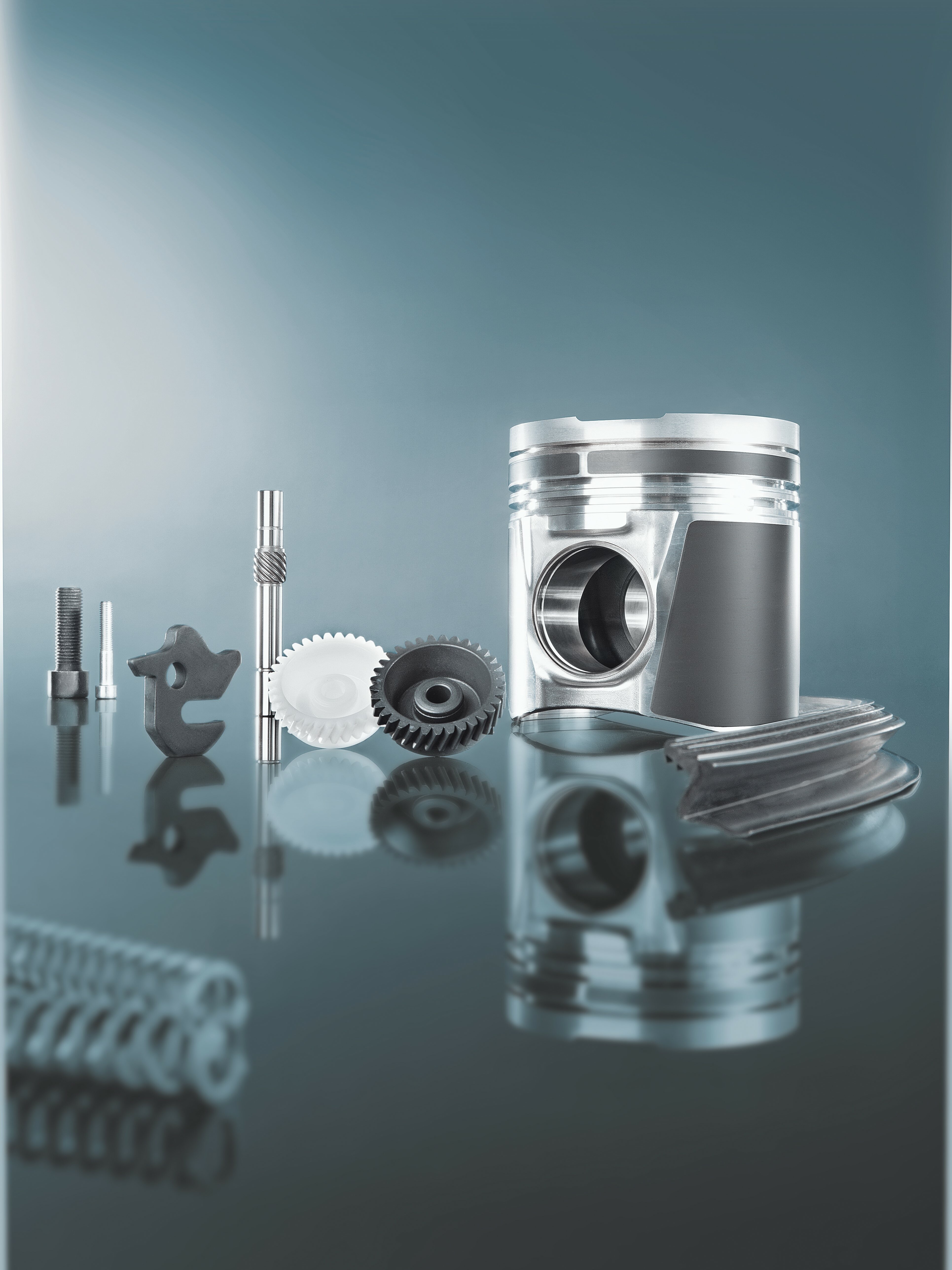
BECHEM anti-friction coatings can be used in a wide range of applications. For example, as dry lubricating films in automated production and assembly or as support for running-in or to improve the emergency running properties of highly loaded machine elements. The anti-friction coatings can act both as an assembly aid or as maintenance-free lifetime lubrication. The wide range of possible applications often requires tailor-made solutions, which we develop together with you in order to minimize wear and reduce maintenance and repair costs. BECHEM convinces with know-how and product innovations as a strong partner.
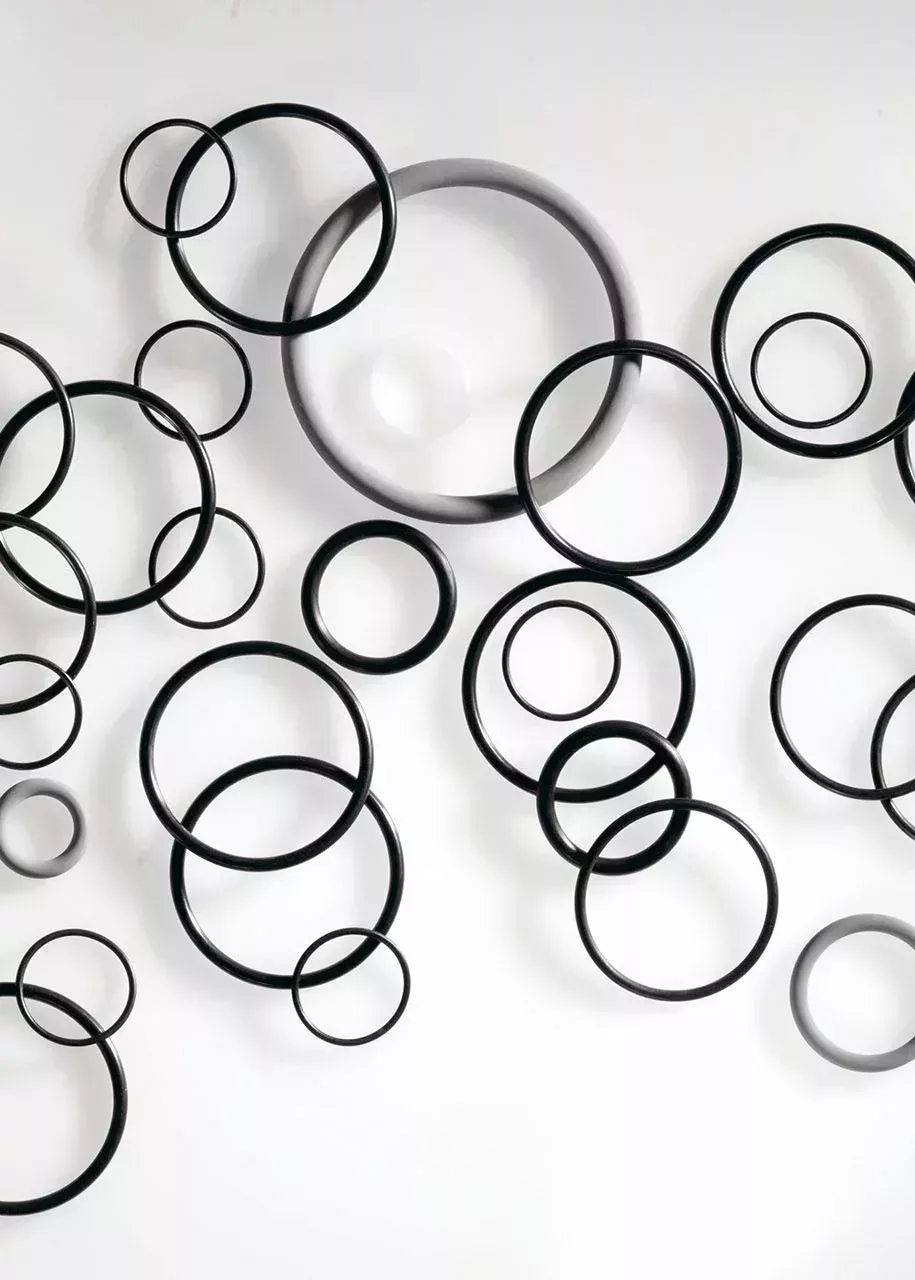
- Reduction of friction and wear
- Constant coefficients of friction with very low scatter
- Use under extreme conditions such as temperature, vacuum and dust
- Temperature resistance ranges from -180 °C to +450 °C, depending on type
- In many cases, lifetime lubrication without oil and grease
- Supports oil or grease lubrication and thus improves the start-up process of machine elements and emergency running properties
- Suitable for all materials such as metals, plastics, wood, leather and elastomers
- Very good corrosion protection
- REACH-compliant products
- Long storage times without ageing effects
- Coatings resistant to mineral oil and chemicals possible
- Clean application - no contamination of friction point and surroundings
- Reduction of vibrational fretting wear (fretting corrosion)
- Thin layers are possible (5 - 30 µm)
- Average yield 15 m2/kg
- No hydrogen embrittlement
- Improvement of the assembly possibilities of machine elements
- Minimization of maintenance effort
- Application methods: spraying, dipping, tumbling, brushing or dip centrifuging on thoroughly degreased surfaces.
- Engine pistons
- compressor pistons
- pumps
- camshafts
- gearboxes
- Locking systems/locking cylinders
- Springs
- Telescopic cranes
- Spindles (small gears, textile industry)
- Slide rails
- Slide bearings
- Leather, fabric
- Plastics (e.g. PP, PA, POM, etc.)
- Synthetic leather (e.g. TPO, PVC, etc.)
- Seals (e.g. EPDM, NBR, FKM, etc.)
- O-rings
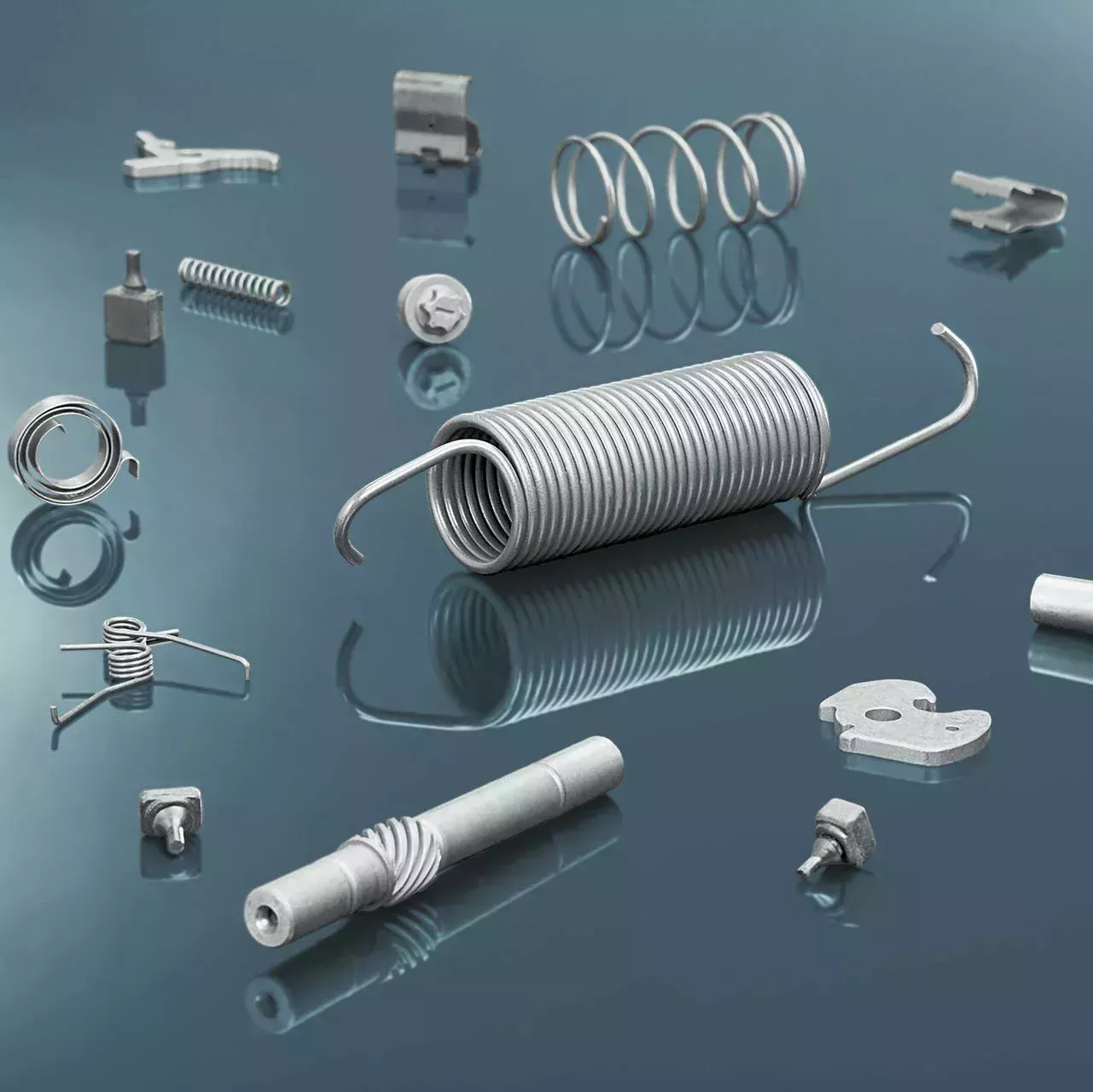
Anti-friction coatings are dry-to-the-touch lubricant solutions that are similar to industrial coatings in their formulation. They are used wherever lubricating greases or oils cannot be used, especially where there is no or only very slow sliding movement. Anti-friction coatings are the ideal solution when relubrication is impossible, extreme temperature fluctuations occur, dirt plays a role or high loads have to be carried with little contact.
The Berucoat AF, Berucoat AK, and Berucoat FX product series impress with a number of benefits, outstanding quality characteristics, and offer individual applications for all areas of industry, especially for bulk goods and mass-produced parts, manufactured from various metallic materials, plastics, elastomers, and leather materials.
Friction-reducing and extremely tough – Berucoat AF
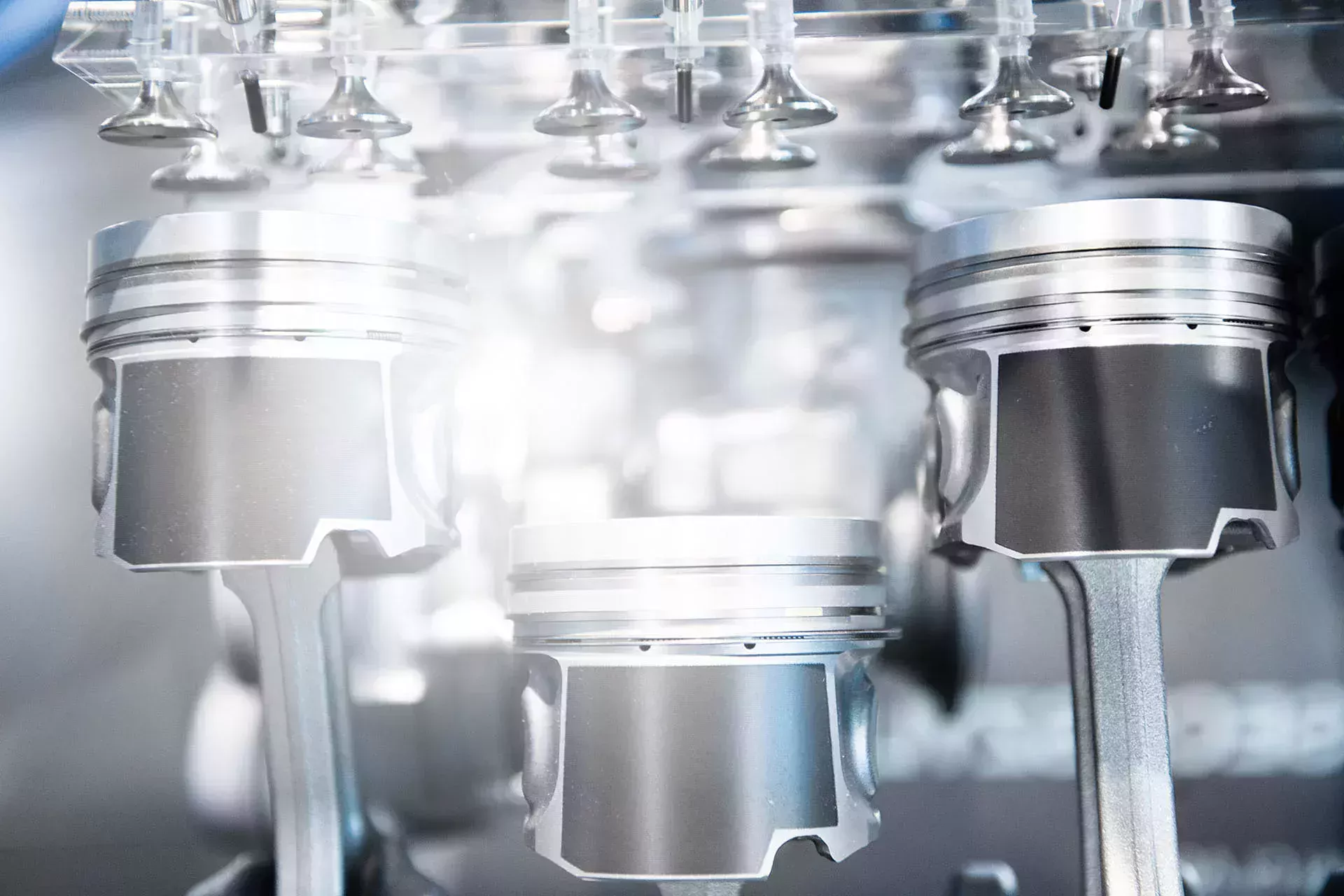
Invisible and noise absorbing – Berucoat AK
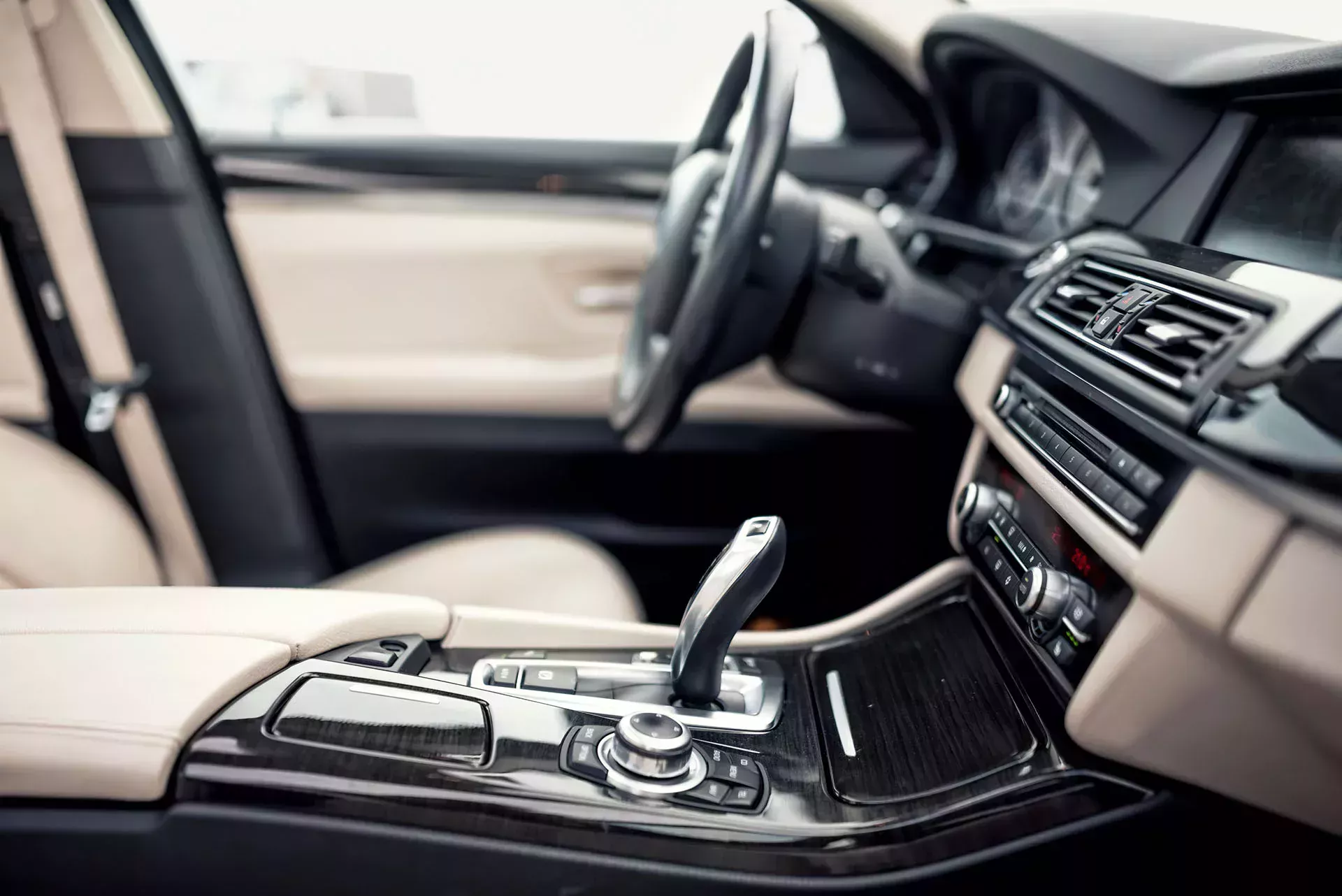
Flexible and abrasion-resistant – Berucoat FX
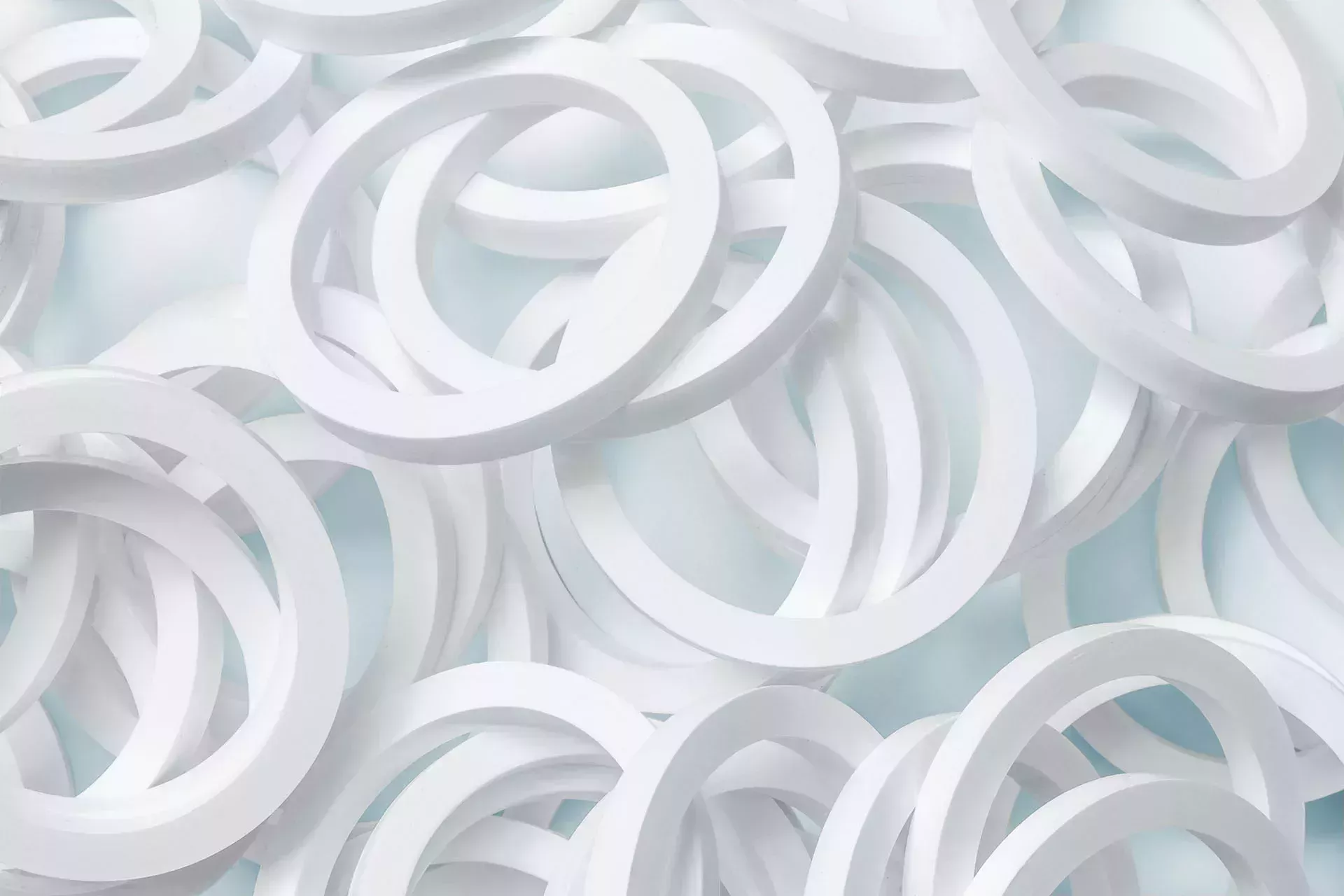
Game Changer: Micro Capsule TechnologyExpanding the functional range of plastics
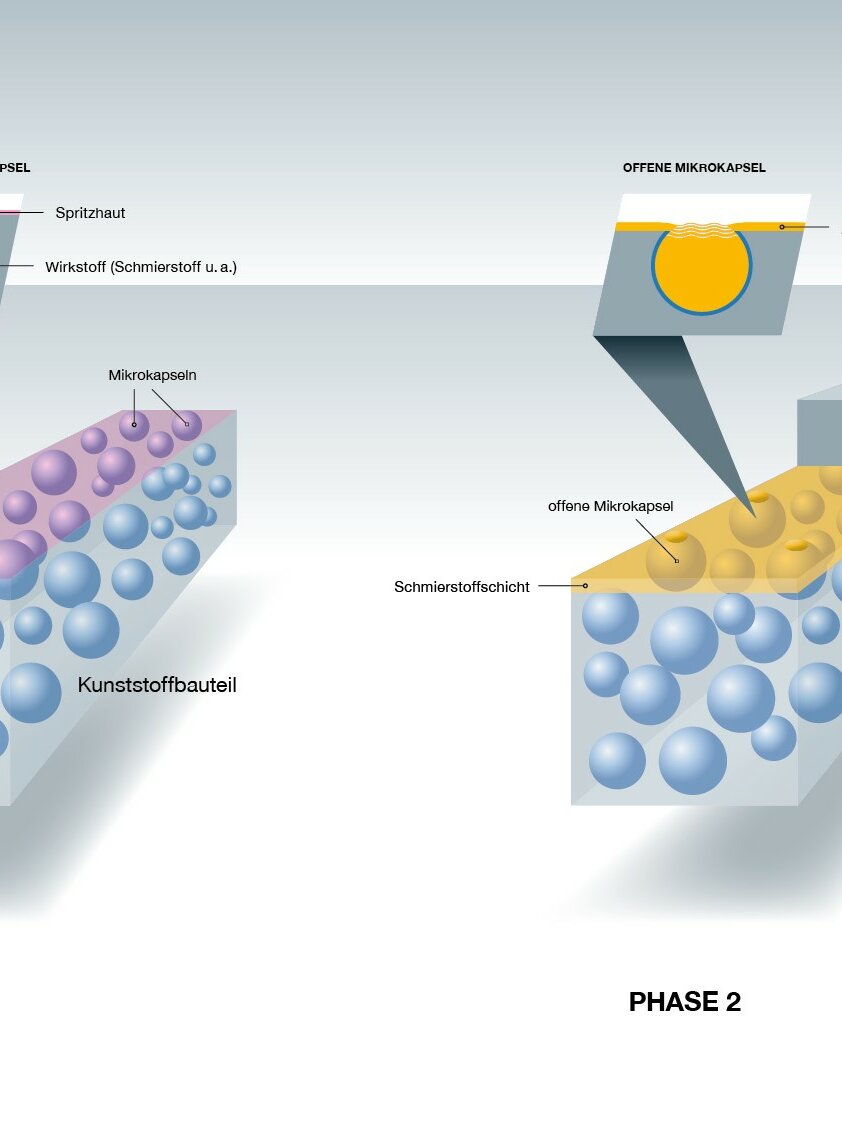
Avoidance of stick-slipwith lubricating greases and anti-friction coatings from BECHEM
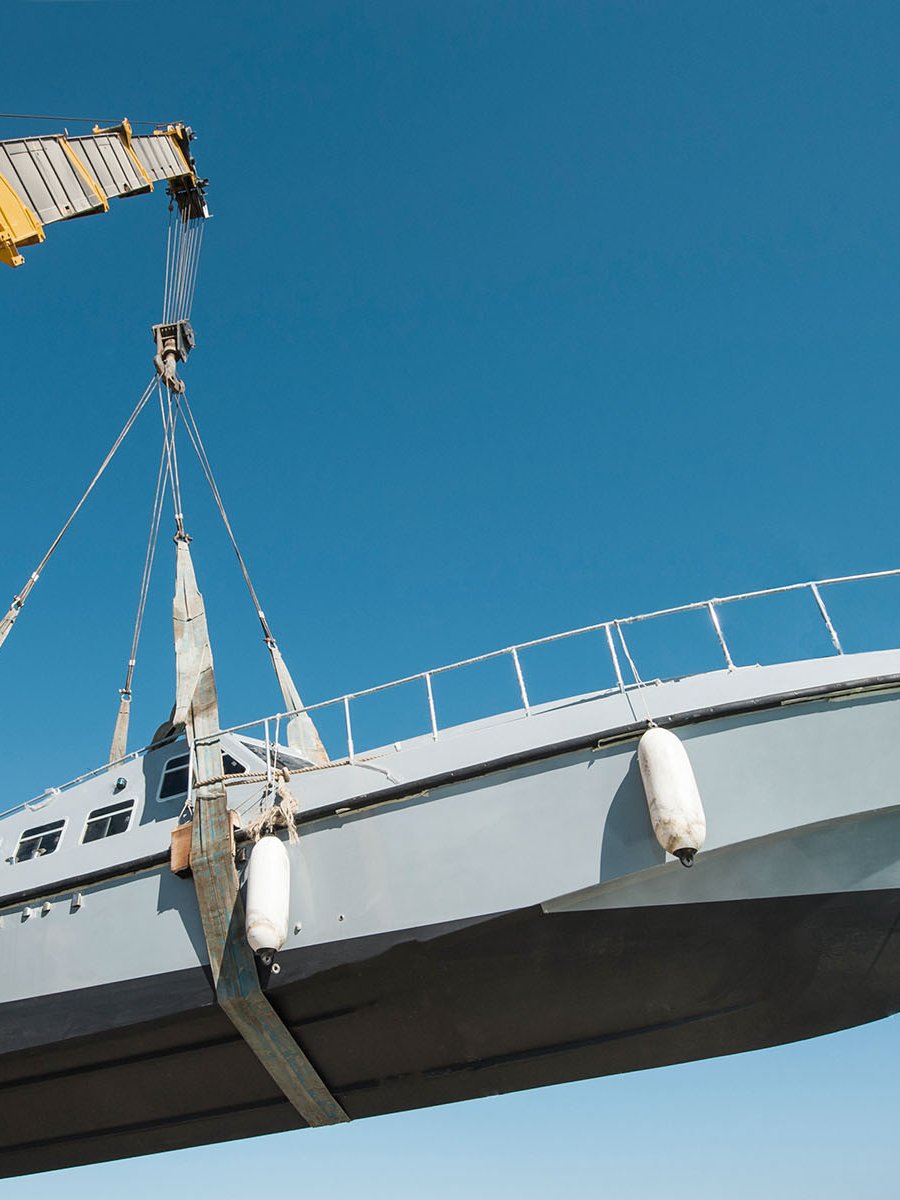