Game Changer: Micro-Capsule TechnologyExpanding the functional range of plastics
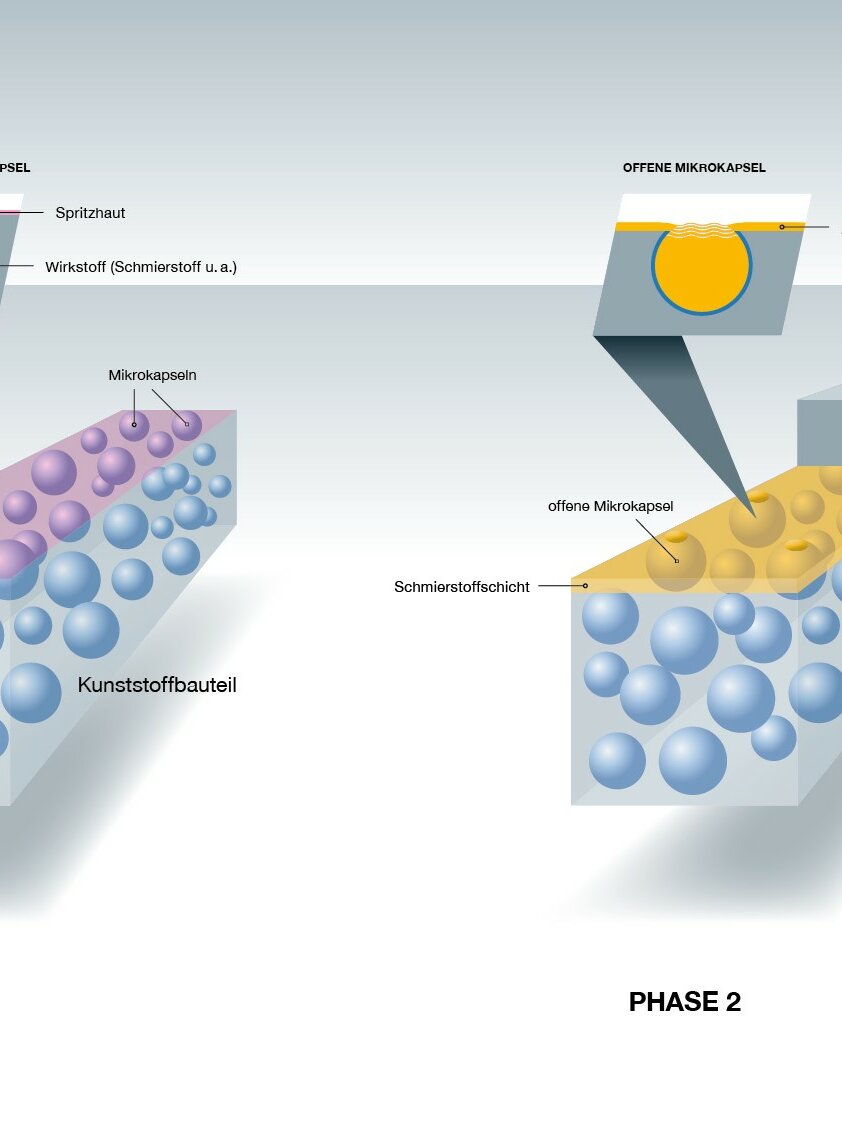
- Convert liquid substances into dry powder
- Encapsulate volatile substances
- Protect substances from reacting with air, light, or liquids, and release them as needed
- Keep highly reactive substances separate from each other
- Release active substances in a targeted manner or over a certain span of time
- Add additional features to a product, such as color or odor
Encapsulating lubricants and active ingredients in a form that is dry to the touch offers the solution to many problems. Through their use in the area of injection molding, micro-capsules are becoming a technological game changer.
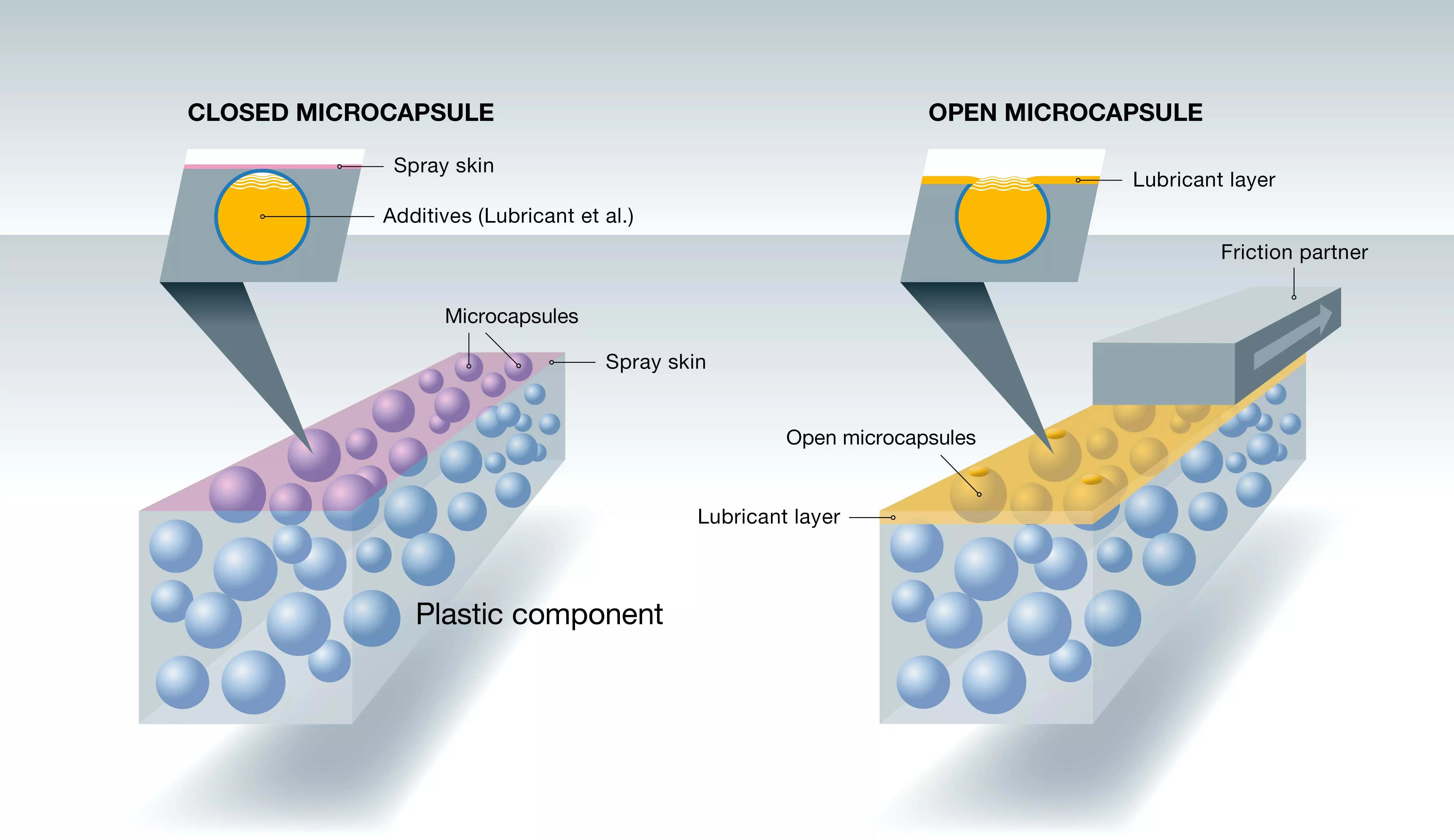
Alongside lubricants, pastes, and lubricant dispersions, coatings are considered to be one of the most effective lubricant systems. BECHEM anti-friction coating systems are indispensable in the mass production of premium motor pistons. Nevertheless, many developers and suppliers are unaware of the full range of possible applications for anti-friction coatings.
These coatings consist of selected solid lubricants dispersed in organic or inorganic binders in a solvent or water. After application and hardening, they form a solid composite of binding agents and solid lubricants. Under tribological load, the solid lubricants are transmitted to the counterbody. This process forms a transfer film that reduces the shear forces and friction values. Several binding agents and solid lubricants are available, including ones that are based on nanotechnology. They feature a wide range of properties to meet the most diverse development requirements.
- Reduction of friction and wear
- Minimizing noise
- Constant coefficients of friction with very low spread
- Can be used under extreme conditions (temperature, vacuum, and dust)
- The temperature resistance ranges from -70 °C to +450 °C, depending on the type
- Mineral oil- and chemical-resistant coatings possible
- Improved running-in of machine elements and dry-running properties
- Excellent corrosion protection
- Clean application – no contamination of friction points and the environment
- Reduction of vibration-induced frictional wear (fretting corrosion)
- Thin layers possible (5–30 µm)
- Many anti-friction coatings can be painted over
- Improved assembly options for machine elements
Micro-capsules (1–1000 µm in size) with active ingredient-filled core material in the anti-friction coating enhance the lubricity of the solid lubricants they contain. The micro-capsules immobilize solid, liquid, or gaseous substances in very small portions, surrounded by a wall or matrix material.
SEM images illustrate the mode of action: Spherical containers in the anti-friction coating, filled with lubricant or other active substances, are only visible under a scanning electron microscope. Under load, the lubricant is delivered to the friction point in metered quantities, where it forms an effective lubricating film and reduces friction and wear. The encapsulation protects against incompatibilities between the resin binding system and lubricants.
Minimal wear can be detected on the surface after every movement. The micro-capsule technology takes advantage of this: The mechanical effect on the anti-friction coating opens the capsule shell, freeing a dose of the additional lubricant. Due to the continuous friction motion in the tribological gap, it is distributed evenly, ensuring a surface that is dry to the touch. With ongoing wear, deeper capsules are exposed, ensuring a consistent supply of lubrication.
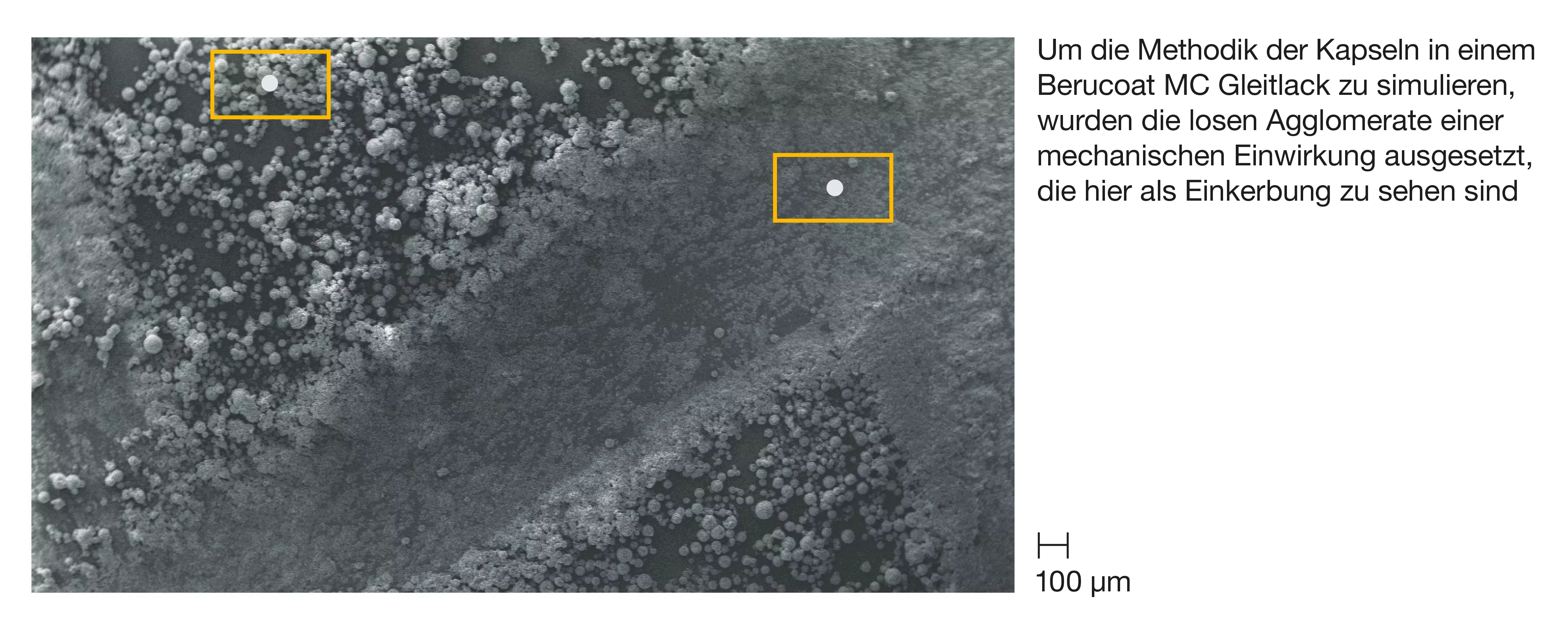
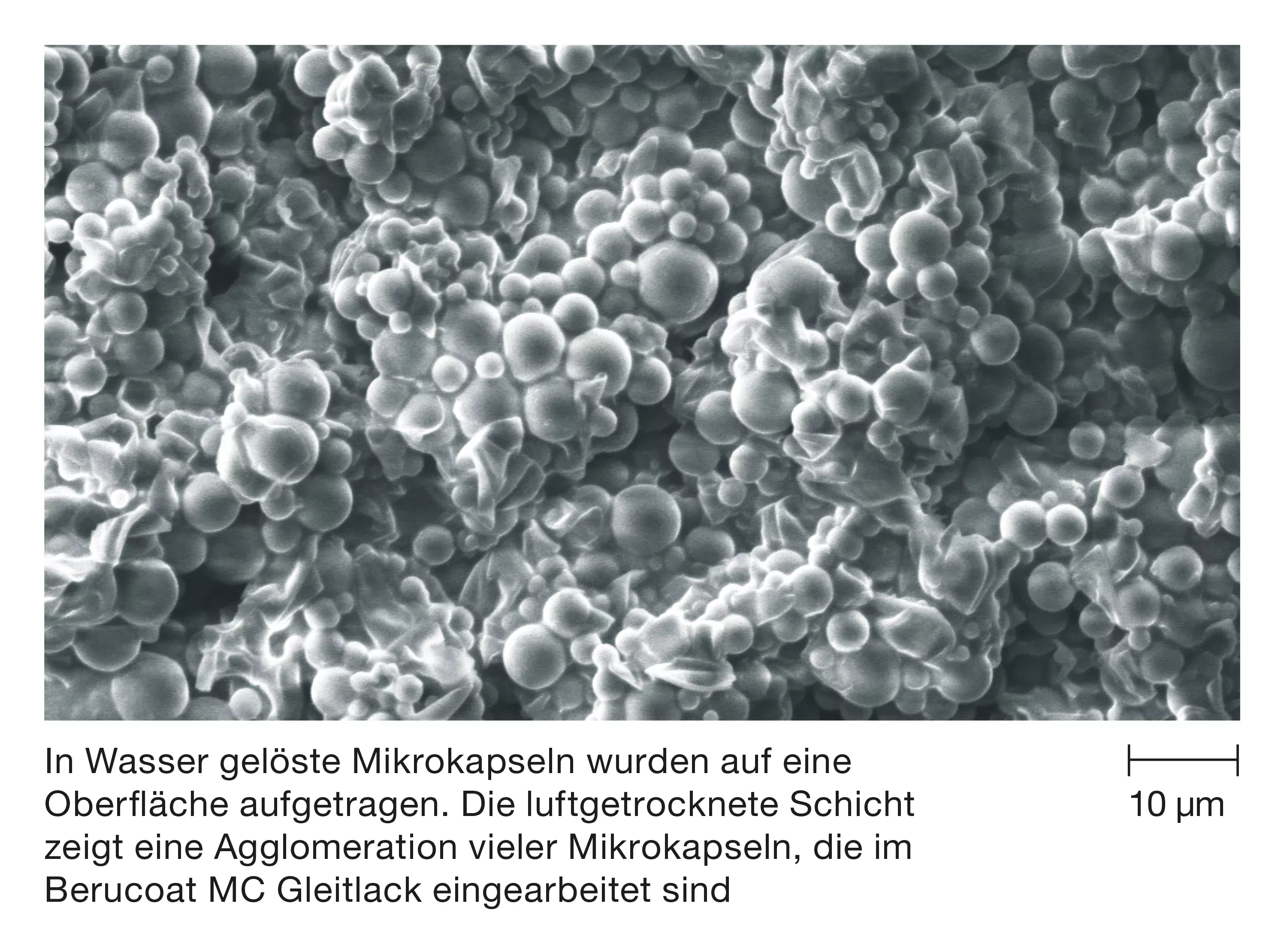
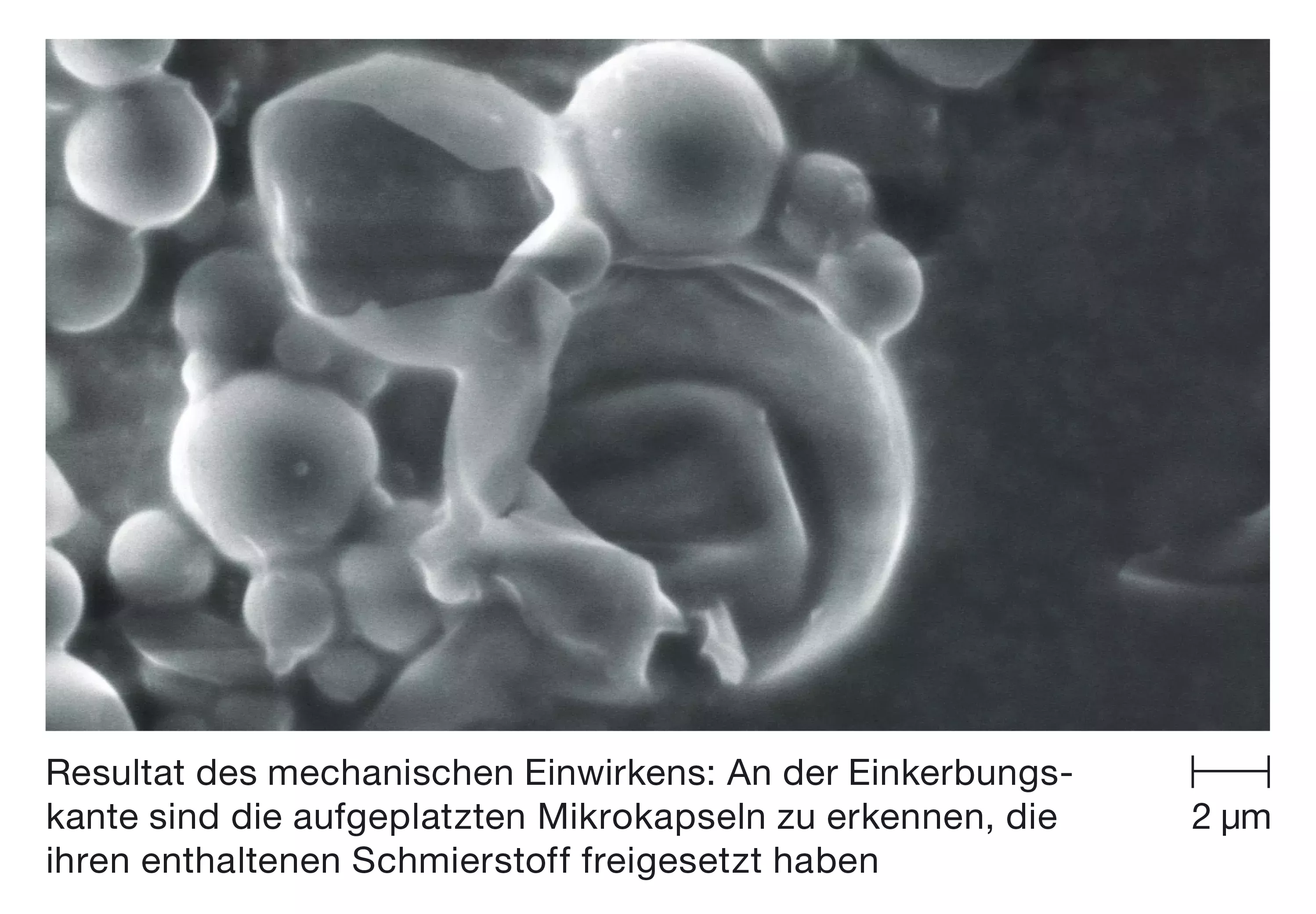
Through compounded micro-capsules, the plastic component receives lubrication as needed during frictional contact. It lubricates itself under pressure, making it a real alternative to graphite or sweating oils.
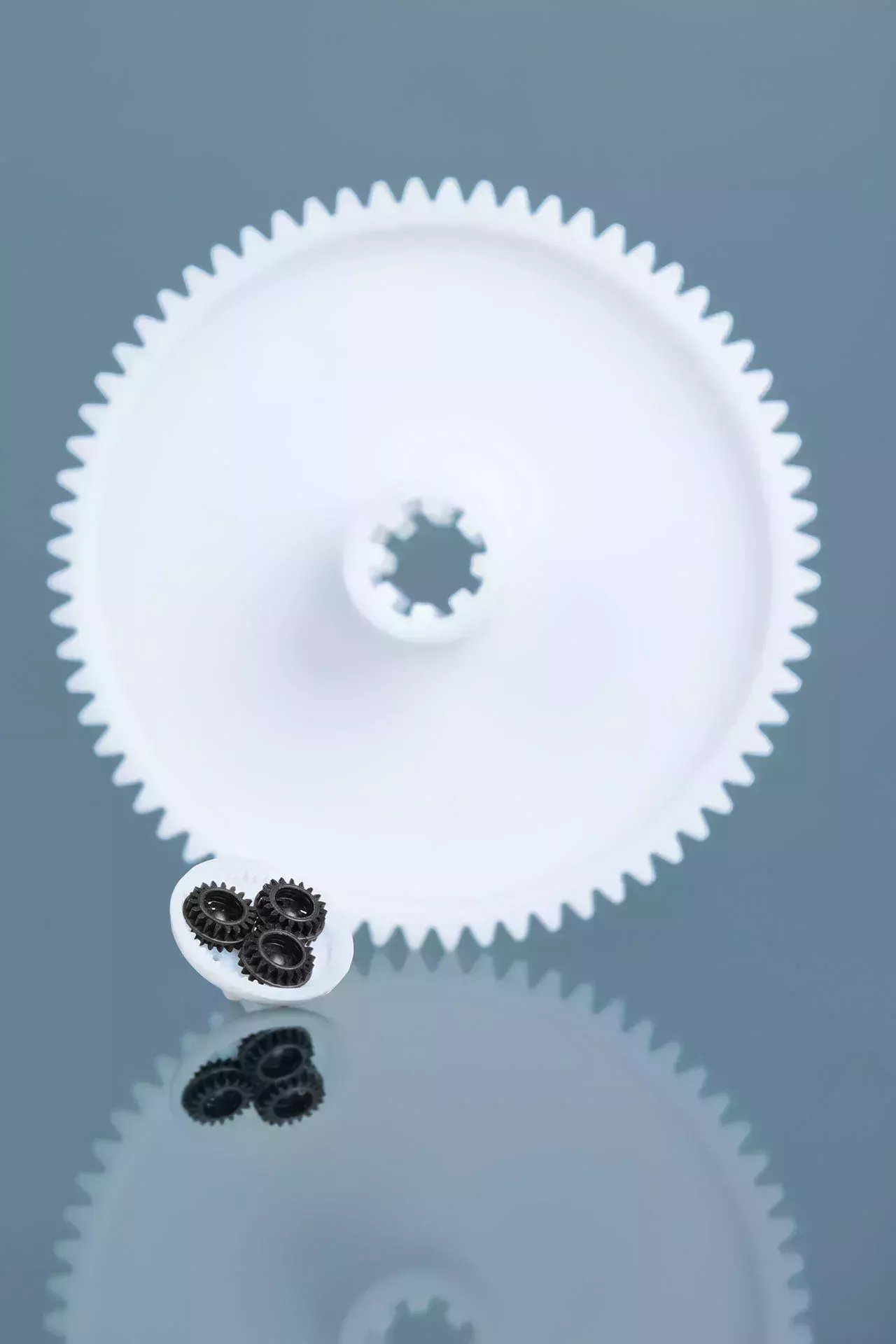
Plastic components are subject to friction and wear in a variety of applications (e.g. sliding doors or plastic gears). Consequently, in an effort to reduce component wear, plastics manufacturers sometimes integrate solid lubricants into plastics. However, only very few solid lubricants are actually suitable for plastics processing. To make matters worse, their use will be significantly reduced again as part of the upcoming PFAS regulation. Conversely, there is a much wider range of liquid lubricants, some of which are even more effective. Unfortunately, they are also difficult to incorporate into a plastic.
This is precisely where micro-capsule technology comes in. Liquid lubricants are encapsulated in such a way that they can be incorporated into polymers as functional substances. All the advantages of liquid lubricity can then play out in the subsequent application in the component. We were able to demonstrate that the integration of lubricant-filled micro-capsules in plastics reduces wear by up to 85 percent. This fact is significant because it clearly improves the efficiency of processes while also reducing microplastics in the environment. Furthermore, the free ingredient selection allows a much wider range of possible applications, from improved components to alternative design approaches.
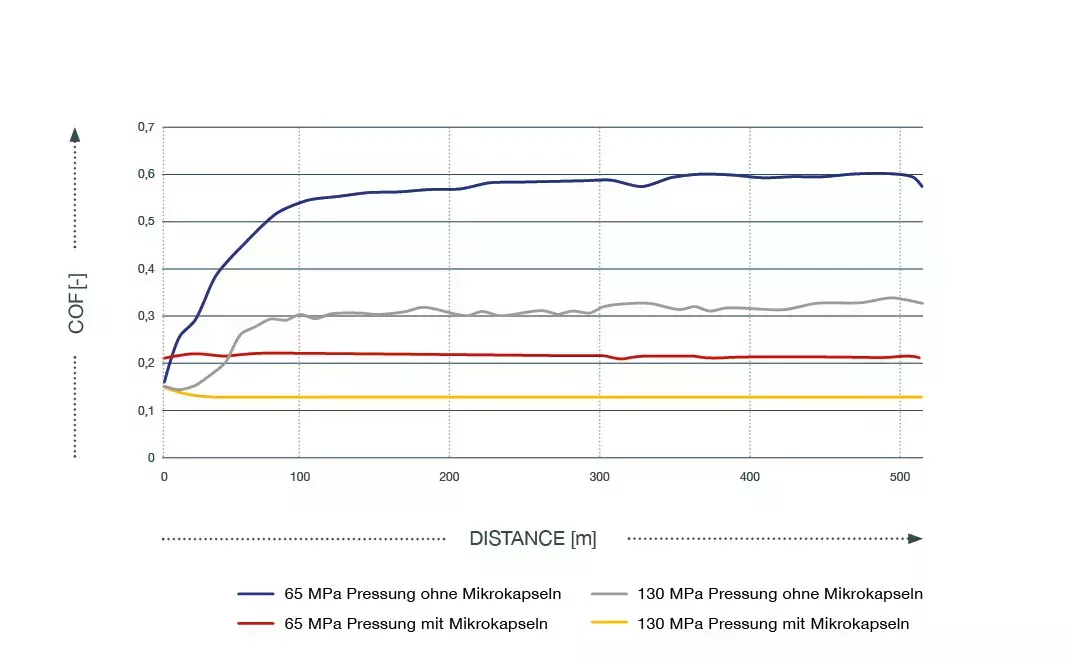
Observing the friction gradient under constant surface pressure shows how efficiently the lubrication at the friction points of plastic parts can be achieved (material POM-C).
Micro-capsules: Huge potential as problem solvers.

Dr. Thomas Löhl
Application Expert Anti-Friction Coatings
We will find the BECHEM solution for your application