Lubricants for sheet metal forming
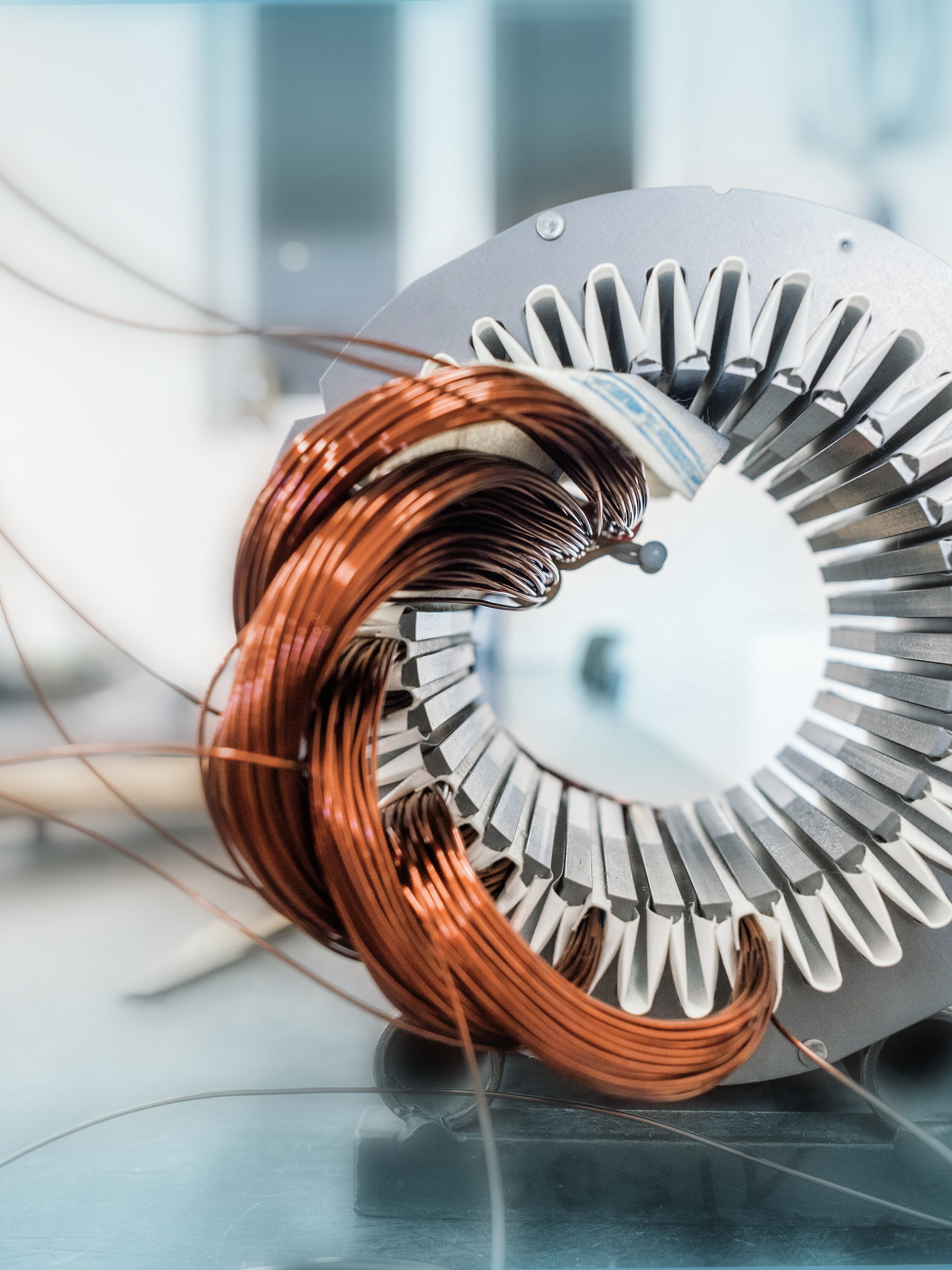
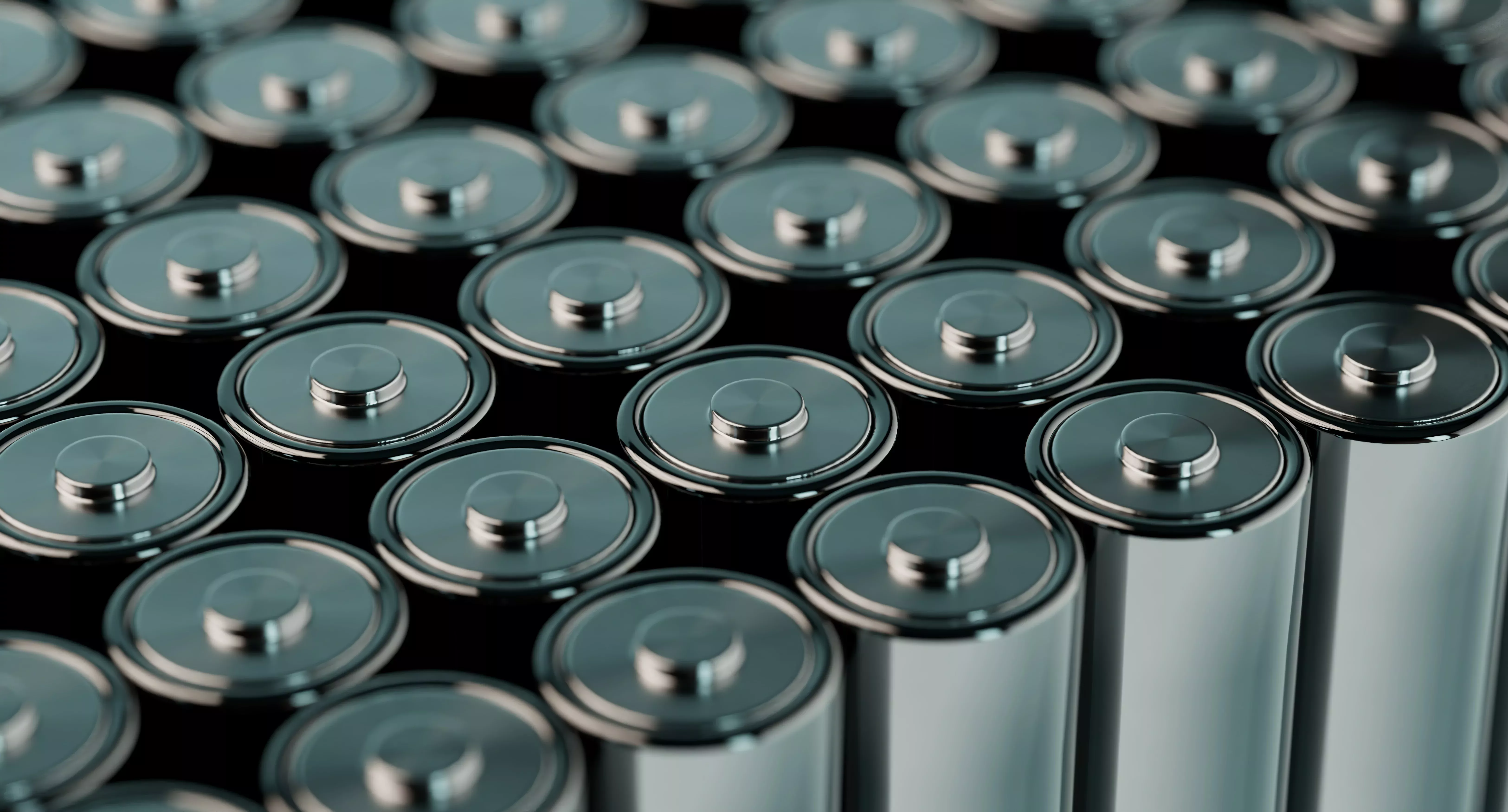
Evaporating punching and forming oils
The BECHEM Form E range is used for simple to medium-heavy stamping and forming processes where low-residue or residue-free surfaces are required. The excellent cooling effect ensures low process temperatures and consistent precision in the production of stamped and bent parts on high-speed presses, for example. Parts produced with BECHEM Form E forming oils can in many cases be further processed without subsequent cleaning. The selection of raw materials guarantees a high level of user acceptance.
Typical applications include modern materials such as copper and aluminum alloys or foils that require spot-free processing. The BECHEM Form E series reliably prevents material build-up on cutting punches.
Non-water miscible punching and forming oils
With the Beruform STO series BECHEM offers products adapted to viscosity and performance: From forming media for simple machining processes to high-performance oils, which are an alternative to chlorine-containing products in the field of stainless steel machining. Besides process safety and economic efficiency, BECHEM makes an important contribution to sustainability by replacing critical ingredients in metalworking fluids.
Water-miscible punching and forming concentrates
The Beruform STE series is always used where the focus is on cooling effect as well as good lubrication performance. The Beruform STE series has been designed for medium to heavy stamping and forming processes. The cleaning of the emulsifiable forming oils is carried out aqueous and is in many cases sufficient with clear, slightly tempered water. Thus BECHEM makes an important contribution to sustainability in production.
Chlorine-free pastes
Products from the Beruform STP product series have been specially developed for forming operations of highly demanding geometries. The pasty, water-washable products are cleaned with slightly tempered water to achieve a high surface quality and an economical production process.
The optimization of industrial production processes top increase economic efficiency is becoming increasingly important. BECHEM lubricants make a decisive contribution here by effectively tapping optimization potentials.
The modern BECHEM punching fluids convince with excellent cooling properties, which ensure both high dimensional accuracy and low tool wear on high-speed presses. Whether in the production of high-quality stamped-bent parts such as hairpins or in the stamping of rotor packages for electric motors: thanks to their individually adjustable residue behavior, downstream cleaning processes can be significantly shortened or even completely avoided.
In the production of precise fineblanked parts, BECHEM lubricants make a significant contribution to a stable process thanks to their balanced additive systems and individually selectable viscosities. A high proportion of smooth cutting, minimal tool wear and long-term process stability, even with large quantities, are decisive factors for the economic efficiency of fineblanking.
- Punching of thin and electrical sheets up to 1.0 mm
- Stamping of rotor/stator packages
- Battery cell housings
- Sheet metal and food packaging
- Electrical contacts
- Bipolar plates
- Steel alloys
- Stainless steel
- Aluminium alloys
- Non-ferrous metals
- Pure copper
- Pure aluminium
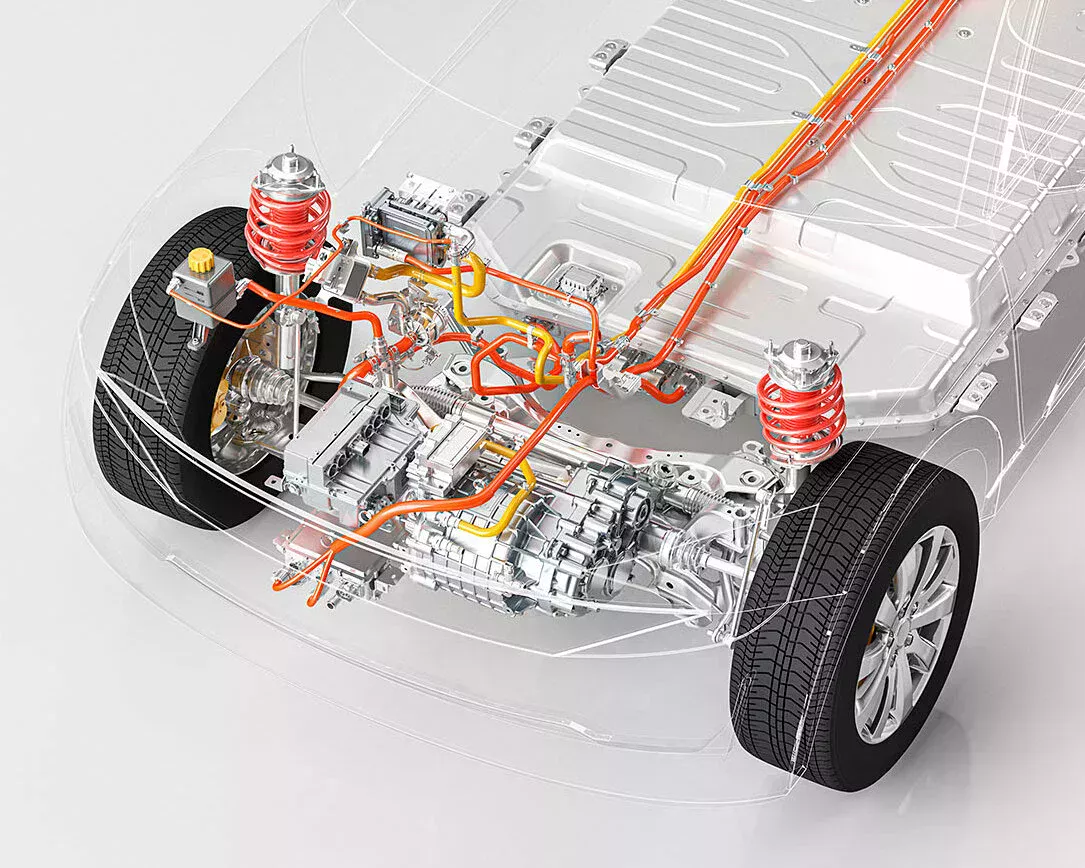

Global Technology Manager Sheetforming